O que é ar comprimido?
O ar comprimido é o ar atmosférico sob pressão. Quando a pressão do ar for maior que a atmosférica, será gerada uma energia por um compressor de ar. Essa energia é distribuída por tubulações.
Na tubulação, parte da energia potencial se transforma em energia cinética, fazendo com que o ar comprimido se desloque até o ponto de consumo. A vazão, portanto, é o produto da área de passagem dessa energia multiplicada pela velocidade do ar (medida em m3/h) .
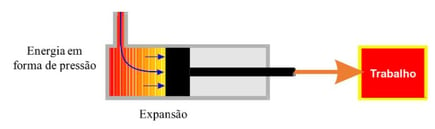
O ar comprimido nas indústrias
O ar comprimido é usado em muitas instalações industriais, seja para o funcionamento de uma ferramenta de ar simples ou para tarefas mais complexas, como a operação de controles pneumáticos.
Abaixo, citamos alguns exemplos da utilização dessa tecnologia para produção industrial:
- Indústria automotiva: funcionamento de robôs e ferramentas pneumáticas para montagem de estrutura e motor de automóveis. Processo de sondagem também depende do ar comprimido.
- Alimentos e bebidas: da embalagem ao armazenamento, a compressão de ar é primordial nesse segmento. Foi criada uma regulação para certificar a qualidade do ar nessas indústrias. Chamada de Classe A, ela é necessária para certificar que não há óleo para lubrificação do aparelho que possa contaminar alimentos e bebidas.
- Medicina e saúde: o ar comprimido é utilizado para máscara de ar em procedimentos cirúrgicos, garantindo ar limpo e de qualidade ao paciente. Além dos sistemas de sucção para remover fluídos ou gases em salas de cirurgia, laboratórios e outras áreas.
- Setor de vidros: sistemas de ar comprimido são usados para realizem pressão dentro de uma garrafa ou farra para a forma final do produto. Além de ser usado para combustão e refrigeração do vidro.
Os tipos de compressores de ar e suas eficiências
Existem os mais variados tipos de compressores, cada um desempenha sua função pré-determinada no sistema. Abaixo, listamos os tipos mais comuns:
- Compressores de Êmbolo – Curso Linear (compressor de êmbolo e compressor de membrana).
- Compressores Rotativos/Compressor Parafuso
- Turbo Compressores / Compressor Centrífugo
Compressores de Êmbolo
Compressor de pistão: contém um êmbolo que produz movimento linear. Ele é apropriado para todos os tipos de pressões, podendo atingir altos níveis de kPa.
Compressor de Pistão de 2 ou Mais Estágios: com este tipo de compressor, é possível atingir pressões elevadas mais facilmente, já que a compressão pode ser realizada duas ou mais vezes, porém é necessário um sistema de refrigeração para a eliminação do calor gerado no processo.
Compressor de Membrana: parecido com de pistão, mas o ar não entra em contato com as partes móveis, uma vez que ele é separado por uma membrana. Assim, o ar não é contaminado com os resíduos do óleo. Estes compressores são utilizados nas indústrias alimentícias, farmacêuticas e químicas.
Compressores Rotativos
O Compressor Duplo Parafuso (Dois Eixos) é, atualmente, o equipamento mais utilizado nas instalações industriais.
Ele apresenta alta vazão e fluxo estável em diferentes condições de pressão. Geralmente, não é equipado com válvulas e não possui forças mecânicas que possam causar desequilíbrio. Com isso, ele pode trabalhar em alta velocidade.
Este tipo de compressor pode ser lubrificado, com um consumo aproximado de 0,11 kWh/m³. Ou pode funcionar sem óleo, com consumo de 0,12 kWh/m³.
Caso o funcionamento desse compressor não seja constante, podem ser implementados inversores de frequência. Desse jeito, é possível economizar energia para que o motor funcione apenas quando necessário.
Turbo Compressores / Compressores Centrífugos
Dentre todas as opções, o compressor centrífugo é o mais eficiente e com menor custo de manutenção.
A compressão é feita pela aceleração do ar aspirado, podendo ser realizada em dois ou três estágios. No processo, a energia de movimento é transformada em energia de pressão.
Essa tecnologia, possui um consumo específico de 0,08 kWh/m³, em média. Sendo assim, ele é 30% mais econômico que o compressor do tipo parafuso.
Por outro lado, não é possível usar um inversor de frequência nesse tipo de compressor, ele precisa ser usado constantemente. Mas é possível usar uma válvula IGV para dimensionar a quantidade de ar produzida em até 3 estágios: de 40 a 100%.
Nesses casos, se, durante a operação, for necessária uma vazão menor que 40%, uma válvula de “blow-off” é ativada e todo o ar excedente é jogado para a atmosfera. Com isso, o consumo de energia será usado para produzir ar comprimido que será descartado.
Por isso, os compressores centrífugos são realmente eficientes apenas para indústrias que precisam usar o ar comprimido em tempo integral.
Outro ponto positivo é que nesse tipo de compressor não é necessário usar óleo.
Qual tipo de compressor é mais eficiente?
A Comerc ESCO preparou uma análise comparativa entre os tipos mais comum de compressores.
Abaixo, apresentamos um caso prático, considerando uma operação com vazão constante de 5.200 m³/h, utilização de 720 horas/mês e um valor de energia de R$0,30/kWh consumido:
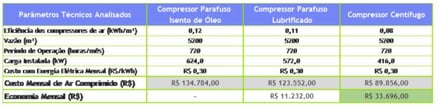
Neste caso, que é muito comum nas indústrias brasileiras, apenas com a troca da tecnologia dos compressores para o ‘centrífugo’, é possível economizar R$33.700,00 por mês. Em um ano, seriam economizados mais de R$400.000,00.
Isso considerando apenas a redução no consumo de energia, sem contar os custos com manutenção que também seriam reduzidos cerca de 40%, trazendo ainda uma maior confiabilidade no processo com equipamentos novos.
Além disso, temos também a redução na emissão de toneladas de CO2 na atmosfera e a isenção de óleo no processo.
Como é a distribuição do ar
Para a distribuição do ar comprimido, levamos em consideração a pressão, vazão e qualidade do ar. Existem diferentes formas de levar o ar do compressor até os pontos de consumo, como:
CIRCUITO ABERTO: o ar flui em um único sentido – impossibilita uma alimentação uniforme em todos os pontos, mas facilita a coleta de condensado;
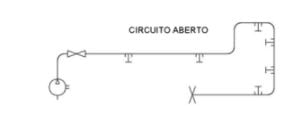
CIRCUITO FECHADO: uma distribuição de ar uniforme e imediato, mas não tem sentido regular de escoamento do condensado. Exige-se mais cuidado;
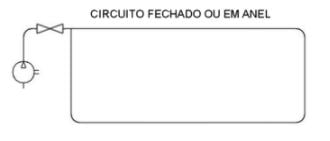
CIRCUITO COMBINADO: devido as ligações transversais e longitudinais, há a possibilidade de fornecimento de ar em qualquer ponto local. Caso seja necessária alguma manutenção em um ponto específico da linha, não é necessário o fechamento total do sistema, mas apenas do segmento a ser trabalhado.
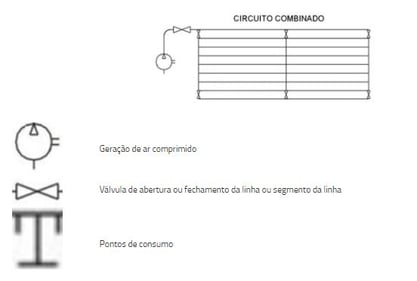
Vazamentos e eficiência energética
O vazamento de ar no percurso do compressor até os pontos de consumo é natural e muito frequente.
É aceitável que uma empresa perca de 5 a 10% da geração de ar comprimido em vazamentos, considerando que o custo de reparação para cada vazamento pode ser maior do que o desperdício de energia e ar.
No entanto, é muito comum empresas desperdiçando de 20 a 30% do ar produzido com vazamentos ou uso inadequado.
São diversos os fatores que levam ao vazamento de ar comprimido, tais como:
problema de qualidade no material pneumático, desgaste natural de componentes pelo uso ou pelo tempo de vida e ainda o relaxamento por vibração de aperto de conexões ou juntas de vedação.
A solução para eliminar estas perdas é implementar um processo eficiente e bem estruturado de localização, identificação, registro e solução dos vazamentos (o popular “caça vazamento”).
Todo vazamento de ar comprimido, desde o menor e mais discreto até o mais expressivo emite um som de alta frequência. Mas, apenas os maiores vazamentos podem ser identificados em meio ao barulho normal de uma linha de produção.
Para alcançar o melhor resultado no “caça vazamento”, é primordial o uso de uma ferramenta adequada que capte as frequências de ultrassom emitidas.
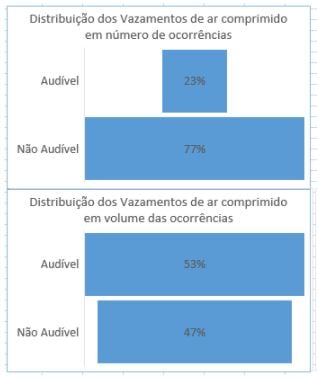
Quanta energia o ar comprimido consome
Cerca de 10% da energia elétrica consumida em uma instalação industrial típica é destinada para a geração de ar comprimido, de acordo com pesquisa realizada pelo Departamento de Energia dos Estados Unidos.
Para algumas outras instalações, a geração de ar comprimido pode representar 30% ou mais da energia elétrica consumida.
Por isso, é muito importante buscar a máxima eficiência na produção de ar comprimido. Em um ciclo de vida de cinco anos, o sistema para essa produção tem custos com consumo de energia, manutenção, instalação e investimento. Conforme abaixo:
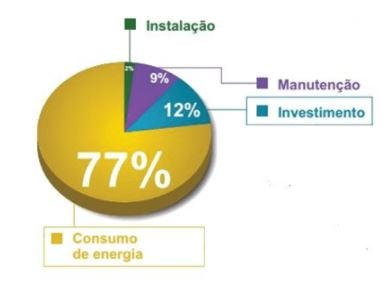
– 12% – Aquisição de equipamentos
– 9% – Manutenção do equipamento de geração
– 2% – Custo de instalação
– 77% – Custo de energia elétrica
Em muitos casos, é necessário avaliar se vale a pena investir em manutenção ou se não é melhor substituir o maquinário. Analisando bem o ciclo de vida útil dos equipamentos usados.
Por isso, ter um programa de manutenção preventiva faz toda a diferença, podendo analisar o melhor momento para troca, reduzindo custos com manutenção e consumo de energia.